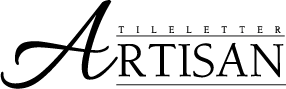
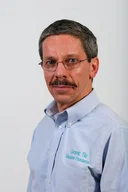
By Scott Carothers, Academic Director
Ceramic Tile Education Foundation
The fit and finish of quality tile work is truly a work of art. While there are numerous ways to achieve a beautiful, finished product, the question is how to do so with accuracy and in a timely manner. Whether the job calls for a mosaic tile backsplash or a large-format tile fireplace, qualified labor, skill, experience, and dedication to excellence are the key components.
When installing tile, one of the most important aspects that the end user will see is layout. If the layout is not centered and balanced or if sliver/skinny cut tiles occur along one side, the job may be rejected. Often when the consumer views a finished tile installation, he or she may not know what is wrong, but something just does not seem right, and the tile industry gets another black eye.
When planning a tile installation, considerable time must be spent on how the finished product will appear. Will the cuts on each side be the same or will the top and bottom cuts be the same? And it does not seem to matter whether the tile being used is small or large.
But how is this accomplished? One way which has gained significant popularity among tile installers is the craft of making and using a template. Merriam-Webster defines a template as: “a gauge, pattern, or mold (such as a thin plate or board) used as a guide to the form of the piece being made. An overlay or something that establishes or serves as a pattern”.
So, what does it take to make a template or pattern?
Installers can be innovative and use many different building materials including ready-made wood lattice strips or other building materials that can be accurately cut into strips such as lauan/luan plywood, foam backer board, or corrugated plastic. Nathan Parsons of The Porcelain Slab Co., in Rocky Mount, N.C., completed his first (templating) job 15 years ago using wood sticks, but now he has switched to corrugated plastic. But Kris Nardone of Nardone Custom Tilework LLC in Kennesaw, Ga., said, “I am not a fan of corrugated plastic, it is not as straight as luan plywood in my opinion.” Vince Parker of Tile by Vince LLC in Havertown, Pa., added, “I use ARDEX TLT XPS Building Panels wallboard. It is fast, sticks with a glue gun, and can be easily modified in place with a knife. I butt the pieces together, then put a block on top to connect them; that helps everything stay in plane. I recycle (leftover) wallboard from previous jobs, so I don’t have to spend for it.”
As you can see, there is little agreement as to what is being used to build a template, but using a template is the key to this success.
The 12” x 24” herringbone pattern fireplace project
Robert Davis of Davis Solutions in Lebanon, Ore. recently installed tile on a large fireplace which included multiple openings. Davis said, “This fireplace had a lot going on with the fireplace itself, mantle, television opening, and speaker boxes. We taped all our Schluter trim in place first, then made a template using Coroplast corrugated plastic . We cut every piece (of tile), then we were able to install all the tile in one day with two guys. All in, I've got 23-man hours into it. [It resulted in] Massive time savings for this large area with a large-format herringbone (tile) and all the penetrations.”
As seen in the attached images, Davis taped all the metal profiles to the substrate, which outlined the perimeter of the project and television opening and constructed the template using thin wood sticks and a hot glue gun. The completed template is then overlaid on the pattern of herringbone tile that was previously laid out, with the cutouts traced onto the tile for cutting.
This project is an excellent example of 12” x 24” large-format tile (Per ANSI A108.T, a tile manufactured in conformance with ANSI A137.1 having a facial dimension greater than 23 in. [584 mm]) utilizing accuracy and the economy of time.
The profiles were temporarily taped to the substrate perimeter and the television by Robert Davis in preparation for the template fabrication.
The template was constructed of thin wood strips that are held in place by hot glue and placed around each opening.
The completed template is overlaid on the previously dry-laid 12" x 24" herringbone patterned tile and traced onto each tile for cutting.
The beautifully-finished fireplace and entertainment center is almost complete.
The marble mosaic tile backsplash
We now move from a large-format tile template to the opposite end of the spectrum with a mosaic tile backsplash that also benefited from using a template. Vince Parker had the job of installing a complicated mosaic pattern of white Italian marble with a round gold dot. Laying this out piece by piece, then cutting each sheet one at a time would have been extremely labor intensive. Parker opted to use a template, which took time to fabricate, but resulted in saving a substantial amount of time overall.
Vince Parker used ARDEX TLT XPS wallboard strips -- which were cut and glued together with a hot glue gun to accurately outline each receptacle and switch -- along with the precise fit to the countertop and the underside of the wall cabinets.
In the attached image, you can see the intricate work of locating all the cutouts in this portion of the backsplash including the electrical receptacles and switches and the offset for the shelf above. Once completed, the templates are aligned on the previously dry-laid mosaic tile for tracing the cuts.
The template was traced onto the marble mosaic tile and cut to fit the backsplash. It is ready to be installed.
The beauty here is that once traced, all cuts can be made at once rather than marking and cutting each sheet individually, which again saves a sizable amount of time and labor. The almost-completed backsplash shows a good top and bottom cut layout, as well as an attractive fit at the inside corner.
Templating has taken a stronghold in the marketplace of cutting and fitting tile in both small and large rooms using both small and large tiles. Creative craftspeople using this technique have made a name for themselves by providing the end user with a beautiful fit and finish, while also saving on labor. Another win-win for the tile industry!
The almost-finished product waiting for grout and sealant. Note the precise fit to the underside of the cabinets and the nice pattern at the inside corner.